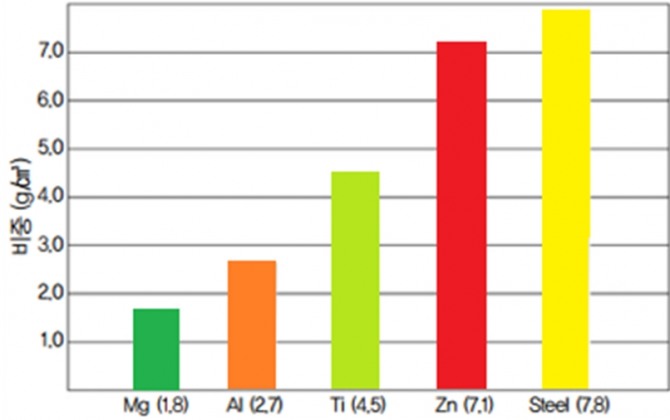
따라서 본 기고에서는 철강 소재를 대체하여 이루어지고 있는, 알루미늄과 엔지니어링 플라스틱 등과 같은 경량 소재와 초고장력 강판를 이용한 자동차 부품 기술에 대하여 설명하기로 하겠다.
■ 알루미늄 소재의 자동차 부품 기술
철강 소재의 대체재로 가장 주목 받고 있는 경량 소재는 알루미늄(Al)이다. 최초의 알루미늄재질의 차체의 스포츠카가 19세기말 베를린 모터쇼에서 소개된 이후 1960년대에 랜드로버의 Buick 215(알루미늄재질의 엔진 실린더 블록 사용),1990년대에 아우디의 A8(전체 알루미늄 차체 적용,239kg 경량화)등과 같은 선진 자동차회사들의 알루미늄 소재의 채택은 꾸준히 진행되어 왔다. 이유는 알루미늄의 다양한 장점에 기인한다.
또한 용접과 같은 접합성에서의 단점을 극복하면서 점차 적용 가능한 범위가 확대되고 있으며 강도를 높이기 위한 합금 기술 역시 발전하였다. 알루미늄에 마그네슘과 실리콘을 첨가하여 열처리한 합금(6000계열)은 인장강도가 높아져 피로강도가 필요한 차체 중요 부위(필라와 사이드 씰 등)에 적용 가능하게 되었다. 인장강도가 250MPa인 이상의 알루미늄 압연 판재를 이용하여 후드, 트렁크 리드 등 차체 부품이 생산되고 있으며 도어, 언더바디, 리어플로어 등의 다양한 부품에도 적용되고 있으며, 인장강도가 400MPa 이상의 고강도 알루미늄 압출 소재는 범퍼 빔, 시트 레일, 각종 멤버류와 임팩트 빔 등의 충격흡수용 부품 등으로도 적용되어 기존 철강 소재와 비교하였울 때 30% 이상의 경량화 효과를 얻을 수 있다.
알루미늄 차체를 적용한다면 완성차 자동차회사는 대규모 투자를 감수해야 한다. 알루미늄 부품을 제조하기 위한 신규 프레스 설비와 조립 라인이 필요로 하기 때문이다. 한 예로 알루미늄 차체는 자성이 없기 때문에 생산 라인에서 자석 대신 진공 펌프로 끌어올려야 하는 생산성 저하의 특성도 감안해야 한다. 알루미늄 판재 가격이 철강 소재에 비해 3배 이상 높은 가격이므로 후가공 비용을 최소화하기 위한 성형가공기술(액압성형, 열간가스성형, 가변곡률압출, 가변단면 압출 등)을 보유하고 있어야 하며, 특히 고강도 알루미늄 판재의 경우 스프링백 등으로 인해 성형이 어렵고 용접성이 낮으므로 공정기술(롤러헤밍, TRB(Tailor Rolled Blanks), 하이브리드 접합 등) 또한 자동차회사들이 보유하고 있어야 한다.
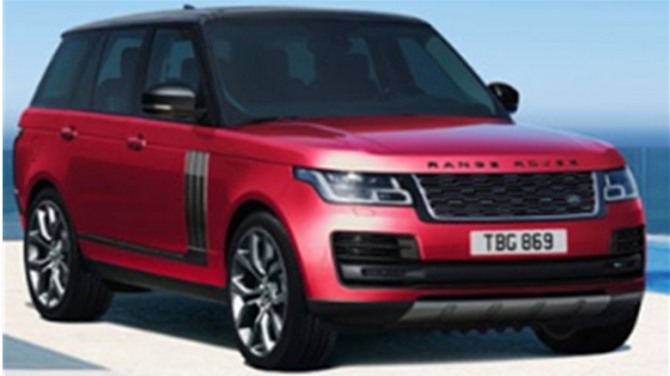
■ 마그네슘 소재의 자동차 부품기술
마그네슘(Mg)은 비중이 1.8로 현재까지 개발된 구조용 소재 중에서 최소의 밀도를 가짐과 동시에 우수한 강성, 비강도 및 비탄성 계수를 갖추고 있ek. 또한 진동, 충격 등에 대한 흡수성이 탁월하고 기계가공성이 뛰어나 자동차 부품의 경량화 소재로서 폭넓게 사용이 가능한 소재이다. 현재 적용 중인 차량용 마그네슘 부품은 실린더헤드커버, 스티어링휠, 시트프레임 등 주조용 부품이 대부분을 차지하고 있다.
한편 마그네슘 부품의 경우도 알루미늄 소재의 경우와 마찬가지로 하우징, 케이스류가 대부분이나 차량의 경량화 효과 극대화를 위해 시트프레임, 카울 크로스멤버 등 대형부품에 적용하기 위한 시도를 하고 있다. 기존 마그네슘이 지니는 문제점인 내식성, 내열성, 성형성 등을 극복하기 위한 새로운 합금 및 공정 개발 등을 통해 판재, 압출재 등을 적용한 차체 부품의 개발이 진행 중에 있으며 최근에는 내열용 소재 개발로 오일팬, 변속기 케이스와 엔진 실린더 블럭 등에 적용분야를 확대하기 위한 연구가 진행되고 있다. 다만 마그네슘은 소재의 가격이 알루미늄 소재에 비해서도 고가이며 생산 공정에서 발생하는 온실가스의 제어 불량률 저감을 위한 용탕 청정화 등 마그네슘 부품의 적용 확대를 위한 걸림돌이 존재하고 있는 단점들이 있다.
■ 플라스틱 소재의 자동차 부품기술
자동차 분야에서는 플라스틱(고분자소재)이 차량 1대당 약 10% 내외로 사용되고 있다. 플라스틱은 경량성, 성형가공성, 저렴한 생산단가 등의 장점을 바탕으로 자동차 내장부품과 외장 부품은 물론 엔진룸의 기능부품, 전자 시스템, 연료 시스템, 에어백 및 안전벨트 등 안전 시스템에 사용되고 있다.
플라스틱은 열에 약하고 깨지는 특성이 있어서 이런 특징이 보완될수록 고기능, 고가의 플라스틱으로 구분된다. 이런 기준으로 구분된 제품은 범용플라스틱과 엔지니어링 플라스틱(EP)으로 나눠지고, 엔지니어링 플라스틱(EP)은 다시 견디는 온도와 강도에 따라 ‘범용 엔지니어링 플라스틱(100~150℃ 미만내열성)’과 ‘슈퍼 엔지니어링 플라스틱(150℃ 이상의 내열성)‘으로 구분된다. 자동차 소재의 플라스틱 전환은 금속을 대체하기 쉬운 부위부터 점진적으로 진행되어 왔으며, 특히 더욱 높은 성능과 복잡한 성형 방법이 요구되는 부위에서의 엔지니어링 플라스틱과 슈퍼 엔지니어링 플라스틱 채용이 확대되어 왔다.
또한, 기존에는 주로 외장재에 대한 관심이 높았으나, 소비자들의 쾌적성에 대한 요구가 높아지고 인포테인먼트 서비스의 등장으로 내장재로서의 플라스틱 중요성은 더욱 커져가고 있는 상황이다.
엔지니어링 플라스틱(EP)은 1930년대 후반 DuPont이 섬유용 재료인 폴리아미드(PA66)을 생산하면서 등장하였다. 1970년대 현재의 범용 엔지니어링 플라스틱(EP)가 시장에 판매되기 시작한 것이다. 미국과 유럽의 화학 소재 업체의 시장 점유율이 전체의 약 50%를 기록하며 선진국 중심 생산 및 공급 구조를 나타내고 있고 최근에는 일본 업체들이 비중을 확대해 가고 있다.
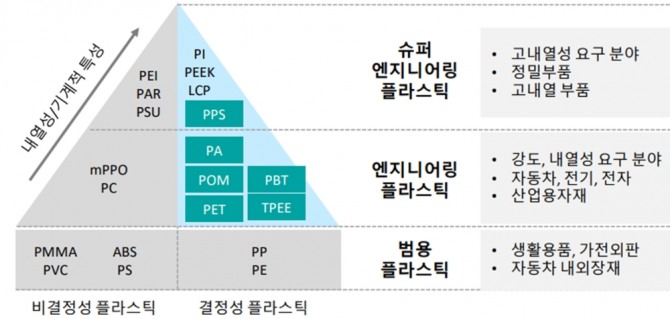
자동차용 폴리아미드(PA)는 내열성, 강도, 내유성, 비용 등 종합적인 평가가 뛰어나 흡기다기관(Intake Manifold), 엔진 커버, 라디에이터탱크 등의 엔진 보기류에 주로 사용되고 있다. 포리카보네이트(PC)는 내열성, 투명성, 내충격성이 뛰어나 자동차용 수요의 약 60%를 차지하는 헤드램프렌즈, 미터판, 각종 내장부품에 사용되고 있다. 또한 자동차 경량화를 추구한 유리 그레이징(Grazing) 및 차체 금속소재의 대체 등으로 활용영역이 점차 확대되고 있는데, 이는 경량화 효과뿐만 아니라 복잡한 형태에 대응하기 쉬운 뛰어난 가공성 덕분이다.
폴리아세달(POM)은 내연료성, 접동성, 내열성에 강점을 갖고 있는 제품으로써, 연료계 모듈과 기구부품 계통에 주로 사용되고 있고 이미 표준화된 소재이다. 금속 소재로의 대체는 이미 상당 수준에 도달한 것으로 평가되고 있으나 그립 및 핸들 기구부품, 연료펌프 등으로 수요 증가가 예상되고 있다. PBT는 주로 하니스커넥터, 엔진 전자제어장치(ECU) 케이스 등 전장부품과 기구부품에 사용되고 있다.
특히, 전기자동차와 하이브리드전기차의 니켈수소전지의 배터리 케이스, ECU 케이스 등에 투입됨에 따라 사용량이 크게 증가하고 있다. 본격적인 친환경차의 성장으로 ECU의 탑재개수가 늘어날 것으로 보이기에 앞으로 PBT 수요 역시 크게 늘어날 것으로 전망한다. 앞으로 엔지니어링 플라스틱의 기술 개발과 규모화를 통해 경제성이 추가적으로 확보가 되면 엔지니어링플라스틱,나아가 슈퍼엔지니어링플라스틱 시장은 점차 확대될 것으로 예상한다.
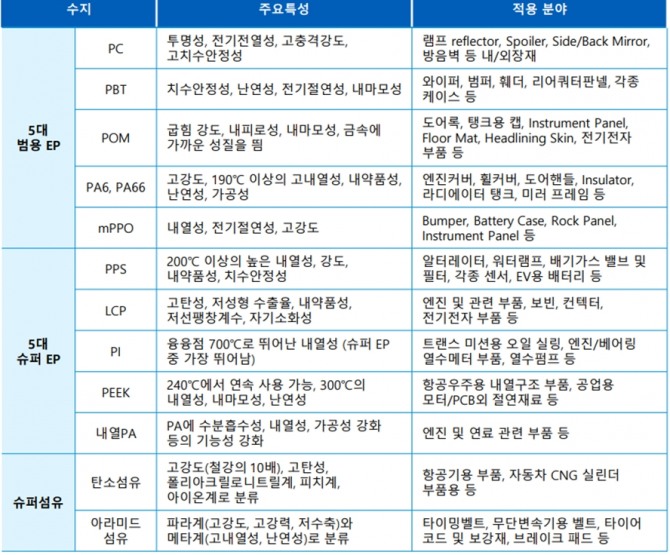
■ 고장력강 소재의 자동차 부품기술
철 소재는 다른 경량 소재 대비 저렴한 가격과 높은 강성으로 자동차의 주력소재로 자리해왔다. 일반적으로 고장력강이란 철강 소재의 인장강도를 500MPa 이상으로 향상시킨 고강도 철강소재를 말하는 것으로 자동차의 안전에 대한 규제가 강화됨에 따라 그 활용도가 높아지고 있으며 또한 기존 소재보다 상대적으로 얇은 두께로 동일한 강도를 나타낼 수 있으므로 사용량을 줄여 경량화 효과를 나타낼 수 있다. 그러므로 고장력 강판과 초고장력 강판은 일반 강판와 비교하였을 때 인장강도를 각각 40%이상(고장력 강판), 100%이상(초고장력 강판) 향상시키므로 부품의 두께를 줄일 수 있으므로 자동차를 경량화시킬 수 있는 대안이다. 초고장력 강판의 경우에는 동일한 강도를 유지하면서 일반 강판과 대비하여 두께를 약 40%까지 줄일 수 있는 것으로 알려져 있다. 또한 우수한 충돌 성능으로 외판 부품 및 구조재에 적용이 증가하고 있다. 2010년대애 출시된 폭스바겐의 7세대 골프는 고장력강판을 37%까지 확대 적용하여 6세대 골프와 비교하였을 때 100kg 중랑을 감소시켰다고 알려져 있다.
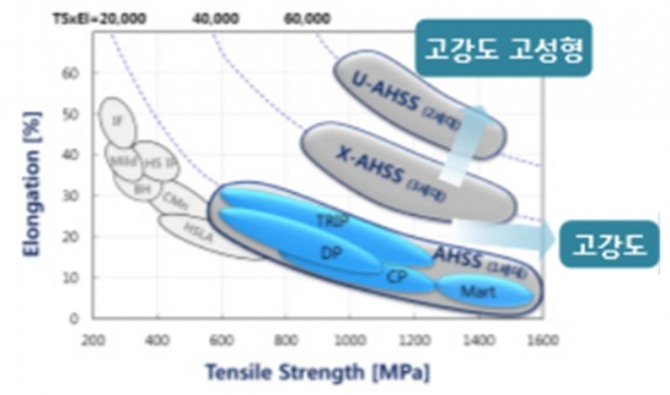
국내 철강소재 기술은 세계 최고 수준을 나타내고 있으며 DP(Dual Phase)강, TRIP(Transformation Induced Plasticity)강 등의 고장력강이 주로 사용되고 있다. 일반적으로 소재의 강도와 연신율은 반비례 하는 것으로 알려져 있는데 최근에는 인장강도와 연신율을 함께 증가시켜 성형성을 높인 TWIP(Twinning Induced Plasticity)강이 국내 기술로 개발되어 다양한 적용이 되고 있으며 또한 인장강도를 1GPa급 이상으로 높인 초고장력강도 개발 되어 있다.
고장력강은 소재가 지니는 높은 인장강도를 이용하여 임팩트 빔, 각종 멤버류 등 충격흡수용 부재, 고강도 부품 등에 많은 활용되고 있으나 성형이 어렵고 금형의 마모가 심하며 후 가공을 위한 용접성, 표면처리 특성 등에 대한 고려도 필요하다. 따라서 다양한 공정개발(하이드로포밍, 핫프레스포밍, 롤포밍 등)과 함께 레이저용접 등의 접합기술 및 도금 등의 표면처리기술이 함께 보유하고 있어야 대량 생산이 용이한 단점이 있다.
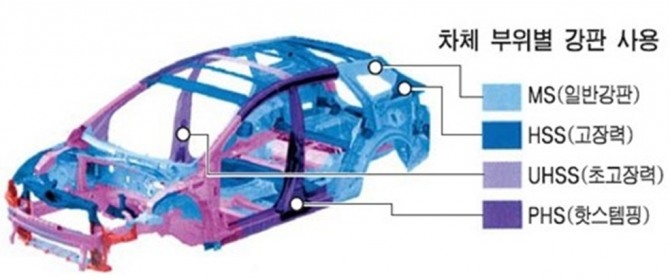
이상과 같이 경량 소재와 고장력강 등의 특성을 비교하면,각각의 우수한 물성과 기게적 성질이 다르기 때문에 소재별 우위를 단순히 평가하기는 어렵다. 예를 들어 탄소섬유복합플라스틱(CFRP)
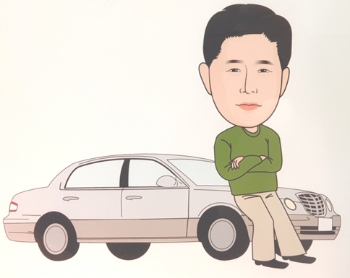
은 비용적인 측면 외에도 이방성 강도,가공성이 낮아 자동차 차체에 100%를 적용하기는 어려우나 부식 저항성 등 물리적 우수성이 높아 금속소재 등와 함께 투입되어 차체의 최적화 소재 구성에 기여할 수 있기 때문이다. 앞으로도 자동차 산업계는 알루미늄 소재,마그네슘 소재, 엔지니어링 플라스틱(EP) 소재와 탄소섬유복합플라스틱(CFRP), 고장력강판 등의 소재 개발과 자동차 부품으로의 확대 적용은 동시 다발적으로 진행될 것이고 차세대 자동차의 경량화를 이끌어 낼 것임에는 틀림없는 사실이다.
한상욱 신한대 기계자동차융합공학과 교수